Optimizing SCADA/Control Systems: Exploring the Strategies and Benefits of Redundancy Implementation
- Rod Nafisi
- Nov 12, 2023
- 3 min read
Updated: Nov 16, 2023
Control systems are the backbone of modern technology, managing everything from industrial processes to smart homes. Ensuring their reliability and availability is crucial, as system failures can lead to downtime, loss of productivity, and even safety hazards. One effective way to enhance the robustness of control systems is by implementing redundancy. In this blog post, we will explore the concept of control system redundancy, its significance, and how it can be implemented to safeguard critical operations.
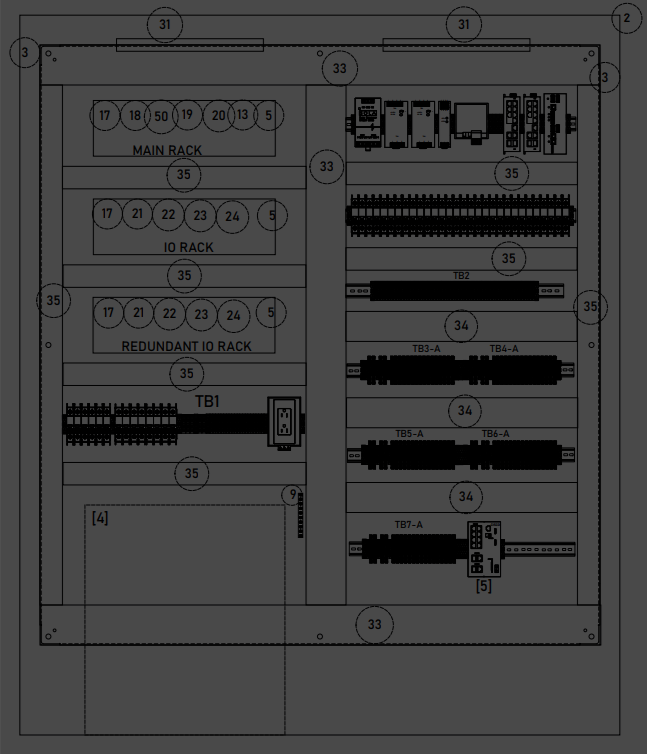
Understanding Control System Redundancy
Control system redundancy involves duplicating critical components or subsystems within a system to ensure continued operation in the event of a failure. This redundancy can be applied to various levels of a control system, from hardware and software to communication protocols. The primary goal is to minimize the risk of system failure and increase overall system reliability.
Why it Matters
Improved Reliability: Redundancy minimizes the chances of system failures, making control systems more dependable.
Increased Availability: Redundant components can take over seamlessly in case of a failure, reducing downtime and maintaining operations.
Enhanced Safety: In critical applications like industrial processes or aerospace, redundancy is vital for ensuring safety and preventing accidents.
How to Implement Control System Redundancy
Identify Critical Components: Start by identifying the most critical components or subsystems within your control system. These are the elements that should have redundancy.
Redundancy Strategy: Decide on the type of redundancy that best suits your system's needs. It may involve hardware, software, communication, or power supply redundancy.
Failover Mechanism: Implement a failover mechanism that detects failures and switches to the redundant components seamlessly.
Testing and Monitoring: Regularly test the redundancy setup to ensure it functions as expected. Implement monitoring systems to detect issues and trigger failovers when necessary.
Documentation: Document the redundancy setup thoroughly, including procedures for maintenance and troubleshooting.
Control system redundancy is crucial to prevent system failures, enhance safety, and maintain continuous operation in critical scenarios.
Case Study: Ensuring Passenger Safety Through Comprehensive Control System Redundancy
Our client, a prominent transit authority, entrusted us with the critical task of designing and constructing a ventilation system control system that prioritizes passenger safety in emergency situations, particularly during tunnel fires.
To achieve the project's objectives, we implemented a robust multilayered control system with the following key features:
Redundant I/O and Voting Mechanism: We ensured redundancy in the I/O components of dampers and fans, coupled with a sophisticated voting mechanism to determine the status of these mechanisms.
Duplicated I/O Points: Duplication of I/O points upon arrival at the PLC cabinets minimized the risk of failure by IO card or chassis, further supported by a voting mechanism to assess point status.
Redundant CPUs, Power Feeds, Power Supplies, and I/O Chassis: Critical components such as CPUs, power supplies, and I/O chassis were made redundant, with CPUs featuring dual Ethernet ports for enhanced data communication reliability.
Redundant PLC Panels: We installed redundant PLC CPUs in two separate panels located at different locations to ensure uninterrupted system operation.
I/O and Data Communication Rings: Implemented redundant I/O and data communication rings to minimize the risk of outages, with all major network switches being redundant as well.
Multiple HMI Systems: Four HMI systems, including two for each location, were incorporated to provide redundancy in user interface access.
Dual Data Gateways: Two data gateways were installed, each serving a location, featuring a voting mechanism to determine the healthy gateway port for data communication. Redundant communication paths to auxiliary equipment like MCCs were established.
Data Gateway Redundancy: To ensure data communication resilience, data gateways were equipped with redundant paths to the Operation Control Center.
Physical Separation: All IO and data communication connections were physically separated and routed through different tunnels, safeguarding system integrity even if one tunnel were to catch fire.
By implementing this comprehensive control system redundancy strategy, we not only met but exceeded our client's requirements, ensuring the maximum possible uptime during emergencies and significantly reducing risks to passengers in the event of tunnel fires.
Conclusion
Implementing control system redundancy to its fullest extent is indeed a formidable undertaking. It demands expertise across various technological domains, spanning networking, data communication, security, hardware, and programming. The complexities involved in ensuring uninterrupted system operation, especially in critical scenarios like tunnel fires, cannot be overstated.
However, the reward for embracing this challenge is unparalleled. The safety of passengers and the reliability of operations are paramount concerns, making the investment in redundancy well worth the effort. By choosing the right partner, one with the requisite knowledge and experience, the risks of incomplete implementation, time overruns, and cost escalations can be mitigated.
In the end, the choice to invest in comprehensive control system redundancy not only safeguards against potential disasters but also strengthens the foundation of trust and reliability in critical infrastructure. It's a decision that resonates far beyond technology—it's about protecting lives, ensuring operational continuity, and providing peace of mind in the face of adversity.
For more information please visit www.avistarts.com or contact us at info@avistarealtime.com
Comments